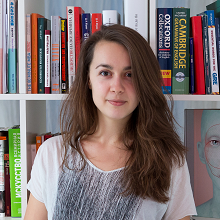
A new interview is with Catherine Kopytina – a young talented designer from Moscow. Her projects speak for themselves – a compact wardrobe for Gogol-center, lamps looking at which you understand that simplicity is the ultimate sophistication. It seems like there’re no impossible tasks for her! About how she did it, and how we printed one of the parts for the famous Light Bean lamp in our interview.
“The word “design” should be forbidden. “Creating a new product” sounds better”, - the guru of industrial design Sergey Smirnov about design and additive manufacturing
About education
- How and why did you decide to become an industrial designer?
Industrial design is only now beginning to be more or less covered design sphere. When I learned that there is one, then I immediately realized – that’s it! I did not have any agony of choosing. I always knew what I wanted to be.
- And how did it showed up? For example, when you were at school?
In details. I always made crafts. Always handmade gifts. Everything was in the complex. You just know the scope of which you are interested. In short, it was obvious. And also when I was a child I wanted to become an inventor.
- How did you choose the place for your future education?
This is based on how I learned what industrial design is. Actually, when I was choosing the university, I started to look for places where design was taught. And I found one institution with industrial design branch. I went to see, to talk to them. They told me everything, and all became clear. So I actually made up my mind about both the university and the profession at one time [Catherine Kopytina graduated Institute of the Humanities and Applied Sciences, Moscow, editor's note].
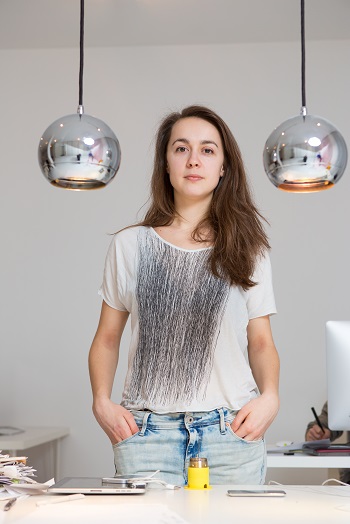
- Once you’ve mentioned that after studying in Milan [Istituto Europeo di Design, editor's note] you realized that the things you had been taught in Russia and in Milan are diametrically opposite things. How did you feel this difference?
Yes, when I was a student, there were no popular live journals or blogs about design. I mean that time industrial design wasn’t so popular. Of course everybody knows already Philippe Starck and Karim Rashid. But there was little information and there was nothing to compare to. That’s why what we made seemed cool to us.
And then you are visiting a country where industrial design has always been. And you realize how everything is done and what for. You are not only making a product that should be good enough to please the others, but also you are realizing the way of making it so that the company which produces it gets benefit at that.
At the present moment the hardest thing to do is to make design to become a part of market. Not only you did realize the project, made photos, everybody is happy, you’re famous and let’s finish with it. No. The thing must be alive. People should really use it, buy it and be satisfied. And the thing should work, be in use, and be cool at the same time.
- How does your profession influence your life? How does it come out?
That’s a difficult question. There always have been critical and exciting parts. Perhaps I see the objects in some other way compared to other people. But on the whole I wouldn’t separate my life and my work finding some differences “before” and “after”. Because all this is tightly linked. Design - it is natural.
- What is the most interesting project you worked on?
All of my projects are interesting. At the present moment the most interesting one is my Light Bean lamp, Light Beanbecause in this project I am not only a designer but also I use comprehensive approach. As far as I work on its production and realization on my own, all this is escalating into much grand scale than I planned.
Well, I weren’t going to work on production of Light Bean but it turned out that it became very popular. Then I realized that I didn’t want to pass it to anybody else and that I want to participate. Thus a company was established around this lamp. And there was so much new to me in this connection that, in general, the project turned out global.
With the search of contractors, producers, with communication with the shops. With what you learn, how this all works, the whole business process. So you understand the correlation between your initial design project and all the other stuff. I mean if you have a mistake from the very beginning in your product, then the whole process of realization isn’t possible at all. That is why the project Light Bean is the most interesting for me now. And I keep it going.
- Could you say that your every new project is more interesting than the previous one?
I would like to think this way. At least it must be like this. Anyway, every project is interesting as far as I don’t have identical projects. For example, I remember A Cloakroom for a Theatre Project (a cloakroom for Gogol Centre, editor’s note). There was that type of a task that I like – to squeeze in something impossible. They wanted to place a cloakroom in a room that was too small for that kind of purpose. I told them: “Guys, do you realize what you want is impossible?”. They were like: “Well, we’re theatre lovers, we need this”. I mean they didn’t realize the problem but it was me who should have fended for oneself. As a result we all were satisfied. And I like this project.
About the peculiarities of industrial design in Russia
- How would you define industrial design today? How do you define it for yourself?
In simple terms, industrial design is the creation of objects, which interact with people. It can be anything from a cup to a mobile phone or a car. Car industry is a separate sphere but it is also industrial design. Overall, everything that concerned – an object and a man, the correlation that occurs between them is design as a rule. Creating an object as such.
Unfortunately, there is one problem… sometimes design is confounded with something else. Design and art are two different things. One must see it clearly. Roughly speaking, a chair in the shape of violin isn’t design, this is a separate thing which we won’t give a name to.
And industrial design is when a chair is made for running it in production and everything should be thought out. It should be convenient in production, the assembling should be thought out. Now there’s a tendency to take into consideration all the stages of a product. For example, if it’s a chair, then this chair has to be easy disassemble and assemble. If it goes out of fashion, and its lifetime is over, then it has to be utilized or used differently.

- Talking about the chairs. For instance, seeing a chair on the Internet from a famous designer, it doesn’t always seem to be comfortable. Then what is it in this case? The chair as an art object or a chair as a correlation between an object and a man?
The answer is included here in task. I mean what was the task when this chair was designed? If it is an office chair, then one of its tasks is to be comfortable, not ornate. It shouldn’t hurt the back while seated. And probably it should be soft.
If it is for example a chair for exhibition, then nobody would say that people would seat on it over 8 hours. That’s why there may be any chair. And it can be called as an object of design. Everything depends on the task.
And by the way the salient feature of design: it solves the tasks. Art doesn’t solve the tasks, except for those which an artist sets himself. While in design there are tasks, there’s a brief that you solve.
- What kind of sense does this term make in Russia nowadays?
Industrial design in Russia now is quite obscure and there’s nothing much to discuss. I can’t say that there was no design in the Soviet Union. There was. But the plants on which all this was done were the plants for heavy not light industry. For this reason, the frying pans are of the good old-fashioned sort. The household articles were produced at the same factories where tanks were made. That’s why either the quality was overdone or the objects lacked elegancy. I don’t want to say that time there were no good industrial designers. Probably there were some, they were called as artist-designers but the equipment and the conditions didn’t allow them to work properly.
Now there are no factories at all. And this is the problem. There won’t be industrial design until culture of life will be returned. We don’t have culture of life as a matter of fact. It was killed in advanced. Nobody understands that everything around could be usable and accurate. Everybody has just got used to it. And it turned out that no one has in mind that the thing could be made convenient for some separate doing.
That’s why design is confused with beauty. People look at Western things, evaluate design for beauty, not realizing that beauty is rather a side effect. If it is not, of course, a chair for exhibition.
- How do you see the development of industrial design in the world - in general and in our country in particular?
Now industrial design is in general in crisis. No one really knows which way to go except of "eco". But with "eco" we have a problem, because no one fully knows what it is. And the market is swamped. Everyone understands that this pace cannot continue. They continue but in fact understand that a very short time is left. Of course, many are reconsidering their attitude now, but I do not know what this will evolve to.
- You are dealing with industrial designers from other countries, for example, with your fellow students?
I communicate with the guys that worked for Matteo Ragni (editor’s note, www.matteoragni.com). And among my Russian fellow students nobody remained in the profession.
- What is the reason?
In Russia, it is clear why people do not stay in the profession. It is very difficult to realize themselves here and it is hard to work. Customers in Russia do not understand why they need it. Very few people realize how much it costs and how much effort it requires. Therefore there are few specialists in Russia. Although somehow there’s enough of them. Our market is just getting ready. I am glad that now in general people know what industrial design is. Before you had to explain.
Regards to the other guys ... For example, in Europe there’s crisis. In Milan, all the factories are closed. This is connected with the financial crisis in Italy and the fact that the productions are moving to Asia. Which was predictable. So there are also young designers often working on their portfolio for several years, and working part time in related fields at the same time, such as graphic designers or write articles about design.
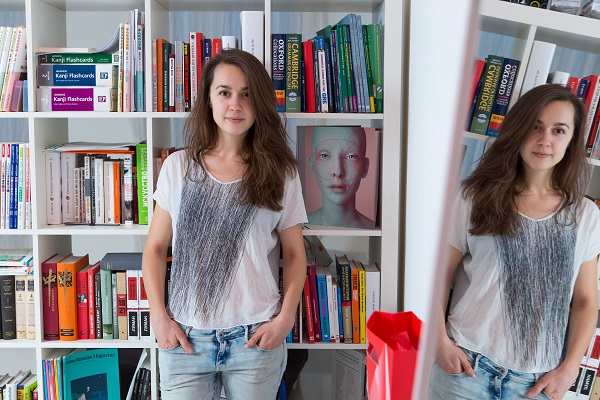
- Could it lead to a situation when all good initiatives of talented people in Europe will just "die out" due to Asia and China?
Well, China is actually isn’t a problem. They are good executors. Here the most important thing is to keep an eye on the process. They will make things exactly of the quality they were paid. Now absolutely all the major productions are already in these countries, in Asia. Smaller productions still remain local.
I produce lamps in Russia, near Moscow. So for me, this is not a problem. Moreover, I see the value that they are produced here. I do not need to go to China. I keep an eye on it by myself. I personally know people who have them grind out, who makes the wire. Small production is likely to remain so. It has its advantages.
Now there are many small studios: in Sweden, in Scandinavia. These Scandinavian companies produce things within their county. And very large ones move to Asia. In Russia producers are quite noncompetitive. For example, working with plastics in Russia is impossible. It’s very expensive. While working with wood in Russia is on the contrary well. So it turns out that big ones are going there, and small ones are here to stay.
- Does this mean that there are more prospects for industrial design here in Russia, since all now are beginning to recognize its necessity and open small manufactures?
Among ourselves we are talking about this advantage for already 5 years. And really, it's either is here or will be. Meanwhile it manifests itself very little. Although the tendencies are excellent. For example, recently published article "30 objects of Russian industrial designers" (article from "Afisha.Gorod", editor’s note). We all came to life and realized that something was going on, because this number we see for the first time. Usually articles are published about three designers or five. But here are 30. We had heated discussions on this topic.
Small manufactures now do everything by themselves, I call it craftsmanship. For example, my friend Sasha Kanygin from Saint-Petersburg (Alexander Kanygin, www.alexanderkanygin.com, editor’s note) now creates and makes everything by himself. And this is the value of his product. Although it is an absolute design product. I think that in Russia all starts from this. And then, you see, it will grow into the mainstream. Then there will be large companies and customers.
About 3D printing and its application in industrial design
We have 3D-printed for Catherine the item from white polyamide and painted it yellow. On this occasion, we learned in detail from the designer how she will use this product and spoke on the topic of 3D printing.
- In what project did you decide to use a prototype printed on a 3D printer?
This item is for the LightBean 2.0 lamp. It reduces assembly time and, in general, makes the assembling easier and better.
The prototype was made to be copied. With the help of it a silicone mold was made and now the copies are made in plastic. In the future I am planning to cast such parts in the mold, but the first few hundred I decided to make this way.
- What impression did the ready part make on you?
I really enjoyed the covering, it was surprisingly velvety. And the color turned out cool. Bright yellow as I wished.
- Do you plan to print anything else in the future? For what purposes and projects?
Yes, I often use 3D printing. For me it is a real salvation, because I do not like and do not know how to do the finishing layouts. The new lamps from the injection material will soon be produced, so that the mould again is going to be made with the printed pattern.
- Have you ever used 3D printing in your projects before? And if yes, how?
I am currently developing a project, which is also associated with lighting. I make a 3D model intentionally, for which then will cast ceramics. Because, for example, the geometric shapes are difficult to do by hand, mold from plasticine.
In general, I have long been using 3D printing. And I know that it is widely used by many industrial designers. Usually prototypes are printed. I recently completed a project where only the first edition was 10 thousand pieces. Of course, it didn’t go without 3D printing.
- Did you like the results you have achieved with 3D printing for the first time?
Yes, of course. The first time is particularly impressive. I love 3D printing.
- If now you could go back in time and use 3D printing technology for any of your completed projects, what and how would you do?
I probably would have made the candlestick "Milto". There are little plastic parts that I cut on the CNC. As a result, when the engineer worked on them, he had already made them in another way, instead of which 3D printing could be used.
- What kind of future do you think 3D printing has in the field of industrial design?
This technology is already being used. 3D technologies have not only good future but also good present already. Everyone I know uses it actively.
For example for the first time I see such great coverage you made in this detail. This is perhaps the novelty for me. I like this "fluffy" effect and dyed items, too.
![]() |
![]() |
In general, the whole world is discussing that every house soon will have a 3D printer. We will not buy things in shops, but simply acquire the files and print 3D models.
- Do you think it's real?
I do not know. I do not really delve into things which are so divorced from my reality. Although I am an industrial designer, now there’s no need for me to have a 3D printer at home.
I find interesting the way of developing it in terms of materials. I've heard that there’s already a possibility to print in stone or bread. This is interesting. Although 3D printing of food is not very inspiring. As for inedible material, it is interesting.
- What advice would you give to your colleagues - industrial designers using 3D printing? Where they can start using these technologies in their work?
I would recommend to make a good 3D model.
- Are all the industrial designers able to work with 3D modeling software?
Not all of them are skilled to build 3D models. But most of them already are. Like at school, children are taught programming since primary classes, designers will soon be able to be proficient in 3D programs. Because they are developed and simplified.
That sounds fantastic that people will draw their own model. But the fact that people can buy ready-made models files and then have them printed is real. Years later it will be possible. But not exactly in the next 10 years. No one will be mentally ready for it.
But the professionals have used it for a long time already.
A piece of personal information
- What inspires you in your work?
I do not know how to answer this question. Everything is simple in this sense. For example, the client says: "I have such a problem." It sounds quite dry. But I do not like to give out banal, uninteresting results. I like solving tasks and make it so cool, so that I am happy, and the client is satisfied. However, it can hardly be called inspiration. But, in fact, it feels alike.
- Can you then say that tasks inspire you?
Yes, tasks are important. Even when a kind of an idea comes to my mind when I saw something, or this something reminds me of something. For example, I think, "it is necessary to make a new lamp", I still set myself tasks. I need to drive myself into the framework. Only then we can get an unexpected result. Such things are not invented just out of my mind. It would never have occurred to me to make a 1.5-storeyed cloakroom. Why? And when there is such a task, then you know what it should be.
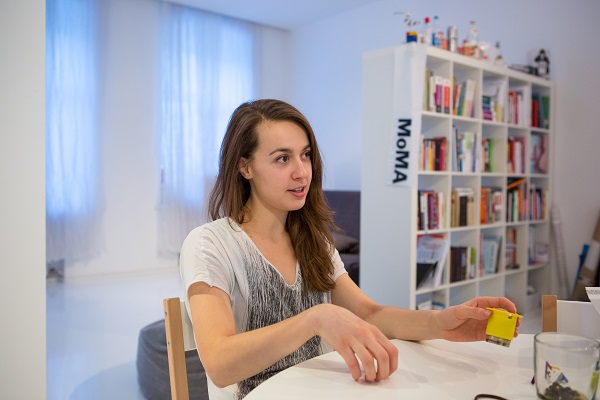
- Do you have a pipe dream in the profession?
Yes, I realize it.
It would be desirable to have a production company and to create items that I myself want to be produced. And then watch people are happy while using them. As for the design consultation, then it is possible to grow indefinitely. It would be interesting to work on the intersection of science and design.
- What are your favorite colors? Materials?
There is no such thing as a favorite color. Color - it's just a tool that you choose when you want. The color does not live on its own.
Among the materials I love wood. Many people like wood. I'll explain why. Because in Russia it is easily accessible, pleasant to touch, has pleasant odor. It's easy to work with.
Casting materials are also interesting to me. I worked with ceramics and cement a little. But I want to try them. The way they behave in the process. I mean making one mould, then another, and pouring material into a mould. The process itself is exciting.
- You have already collaborated with such brands as Lavazza, Jannelli & Volpi, Fabbrica del Vapore, Campari, W-eye, Cartier, Disney, Bell'Arte and others. What are the brands, the companies you would unconditionally agree to work with if you were offered? Why them?
With Campari - with pleasure. They are cool guys. They have the whole giant company, they produce not only Campari drink, but also related items: bottles, furniture for their cafe. How did I know them? - When I worked in Italy in the design studio of Matteo Rania, we had a lot of projects related to Campari. They even produce their books. We designed chairs, tables, benches for them.
They have, in general, a very significant bottle. It was designed in 1932 by the Italian Futurist painter Fortunato Depero and design since then has not changed, but they have been doing all sorts of new and interesting things for a small bottle. For example, Matteo made an accessory for the bottle so that it stands at the bar and lookes like a glass. Very inventive.
- Among industrial designers who do you align with in your creativity?
Probably I can tell you nothing new. I like Achille Castiglioni, Ronan & Erwan Bouroullec. I like the Scandinavian Note design studio very much. Italian Luca Nichetto. By the way, he has just released a new stunning tea set together with Lera Moiseyeva. This is very encouraging.
Although the Italians are now less popular. British Edward Barber and Jay Osgerby (BarberOsgerby design), they made the Olympic torch for the Summer Olympic Games in London 2012.
- What would you teach those guys who today want to devote themselves to industrial design?
Not to finish the project on visual 3D model. Be sure to do a physical model to understand how it works. For now there’re just too many people who make 3Dmodels and just finish with it. But this is not the most interesting. The most interesting is to see the result in the physical world. And then they understand themselves what they have done. Whether it is cool or not.
Author: Daria Kazovskaya
Photo: Maria Andreeva
website: katerinakopytina.com
“I want industrial design to originate appear in Russia” – Michael Belyayev sharing his point of view on profession